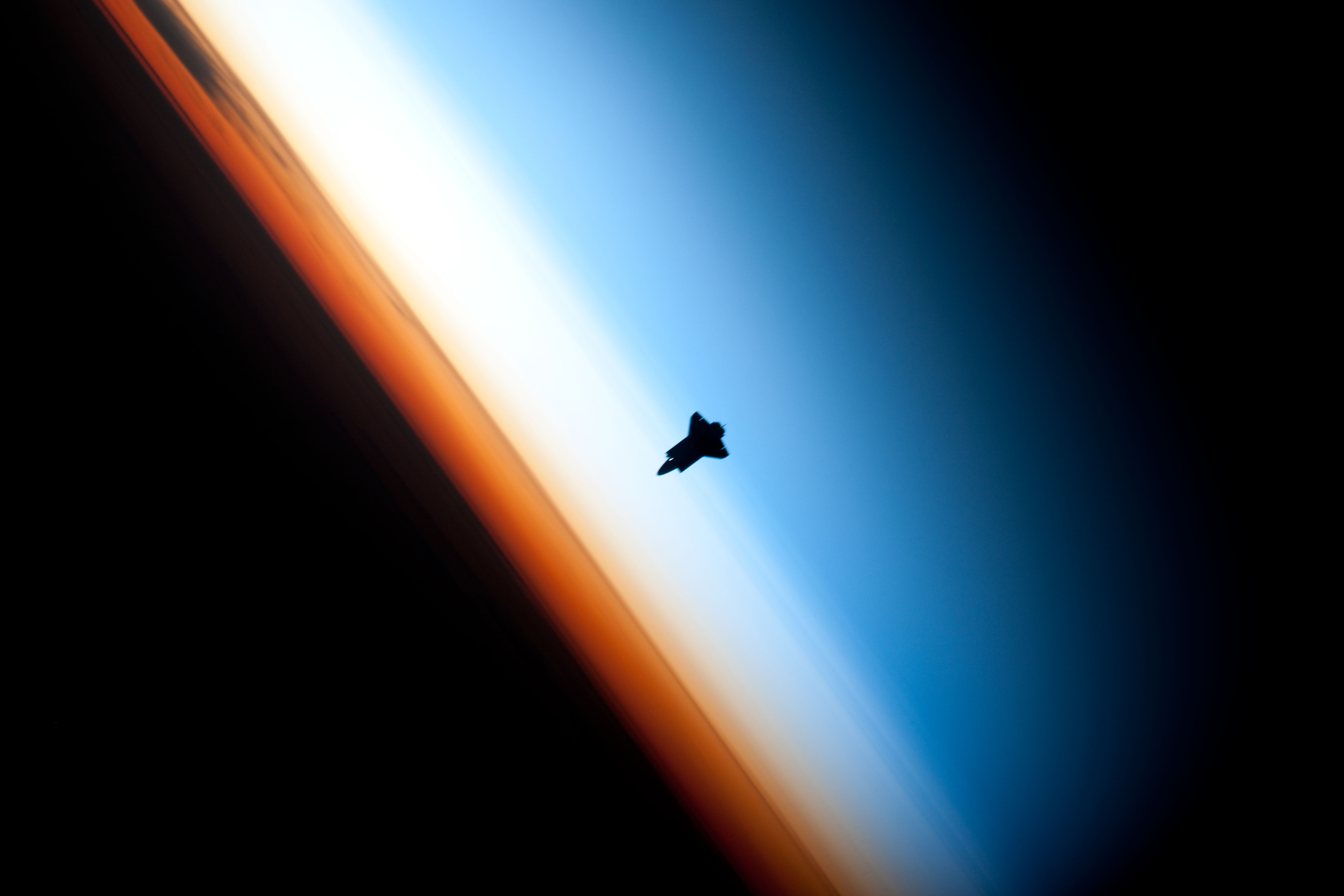
A space shuttle silhouetted against Earth’s horizon. Credit: NASA/Crew of Expedition 22, Wikimedia Commons.
From July 16 to July 22, 2018, the usually mellow tarmac of Farnborough Airport in Hampshire, UK played host to one of the largest airshows in the world – Farnborough Airshow 2018. More than 1500 aerospace firms from 40 countries participated, each vying for attention for their latest technologies and products.
Away from the thunderous aerobatic displays and overshadowed by Airbus’ and Boeing’s blockbuster $57 billion and $82 billion deals announced there, however, another group of companies – the additive manufacturing firms – were creating their own commotion.
A New Voice in the Crowd
During the airshow, industry heavyweight GKN was ready to showcase its 3D printed fan-case mount ring for aircraft engines. In an interview with AINonline, Russ Dunn, GKN’s senior vice president of engineering and technology, claimed the process – which would dramatically cut material volume and cost – had reached production readiness.
Indeed, efforts to produce advanced aircraft interior components with additive manufacturing is growing at breakneck speed. Today’s F-18 Hornet fighter jets, with their original design stretching back to the 1970s, have 90 3D printed components. The F-35 Lightning II, designed at the turn of the 21st century, features 900 of them.
Truth be told, in the cautious aerospace industry, most additive manufacturing efforts are still in the prototyping and testing phases. It is only very recently that parts are being certified and applied to flight systems.
Nonetheless, looking at current trends and growth rates, there is little room for doubt – additive manufacturing is the future of aerospace.
Additive Manufacturing Addresses Aerospace Innovation Requirements
It is not by chance that additive manufacturing is making its way into aerospace. Using 3D printing for aircraft and spacecraft component prototyping can help firms address some of the key pain points hindering innovation and product development.
- Strong and Lightweight Materials
Materials play a vital role in flight performance for air and spacecraft. Many contractors are interested in replacing metallic alloys with composite materials that are lighter and equally strong. For example, SpaceX’s Falcon Heavy uses carbon fiber built upon an aluminum core in its interstage that connects different stages of the rocket together, while its fairing is constructed with carbon fiber reinforced polymer.
In the field of additive manufacturing, technological advancement has allowed for printing of mesh and lattice structures that provide the same strength and utility with less material used, thus reducing both cost and weight. This can serve as a complimentary method for aerospace manufacturers to lightweight and increase material strength of their crafts.
- Complex Components and More Functional Parts
Advancements in aerospace technology have increased demand for ever more complex components not easily produced by conventional subtractive manufacturing. To fit more features into a compact and streamlined airframe, new functional parts customized for specific needs are also highly sought after. Additive manufacturing is a go-to technology when reducing part-count as well. Fewer separate parts means less assembly, fewer failure points, less weight and ultimately leads to greater part reliability.
With complexity and functionality being two main foci of 3D printers as well, it is unsurprising that the two industrial fields have been developing in tandem in the past few years, with major collaborations between 3D printing firms and aerospace giants such as General Electric.
- Time and Cost Reductions
As in most industries, it is advantageous for aerospace firms to cut costs and lower lead times without sacrificing innovation and productivity.
Additive manufacturing opens the possibility of rapid prototyping and small-scale production in-house, in smaller workshops and even in the field. Therefore, engineers no longer need to send prototype designs to external facilities for manufacturing, thus allowing for immediate component testing and design iteration, potentially drastically cutting R&D time frames. According to Raytheon, this can change the entire logistics equation allowing for ‘just-in-time’ manufacturing and potentially manufacturing in the field, at the point of need.
3D printing also does well to reduce material costs, since an additive process removes the need to start the manufacturing process with more material than needed and subsequently etching and wasting much of it away. The in-house production capabilities enabled by industrial 3D printers also allow companies to stock fewer spare parts, thus reducing inventory costs. Lastly, R&D costs are kept low with economies of scale rendered irrelevant by the ability to change designs frequently with only minor setback for each design failure.
With reduced costs and time, there is a lower barrier to entry for new firms to join the R&D process, potentially accelerating the pace of aerospace development.
The DragonFly Pro Advantage
Currently, there are several big players specializing in aerospace additive manufacturing, leading the charge towards better materials, designs and features. However, in a field where outer space is the limit for innovation and discovery, many opportunities remain unexplored.
Nano Dimension offers aerospace firms capabilities to produce functional electronics through concurrent multi-material 3D printing. This type of printing offers several unique benefits:
- Rapid PCB Fabrication
All modern aerospace crafts are heavily dependent on electronic systems for vital operations such as fly-by-wire mechanisms, radar, cockpit displays and flight computers.
PCBs are an essential mainstay of such systems. Improving the performance of critical PCB components can improve flight performance of air and spacecrafts, while the harsh environmental conditions some PCBs face in flight means that there is no room for design flaws. Furthermore, in combat theatres, such as on an aircraft carrier, there is also the need to quickly produce new “limp-home” PCBs near the point of need so that aircraft systems remain serviceable.
Given these circumstances, there are few other situations where rapid PCB prototyping and fabrication is more critical.
Nano Dimension’s flagship DragonFly Pro 3D Printer aces at addressing these challenges by offering unprecedented flexibility, security, and speed for rapid PCB fabrication. With a complete suite of dedicated software, award-winning inks and the DragonFly Pro printer that concurrently prints both conductive and dielectric inks for each PCB layer, fabrication and prototyping can be done securely and reliably in-house while taking no more than a day for many parts.
The benefits are immediately obvious when compared to a traditional workflow, where the PCB designs are outsourced for printing – entailing significant transport costs and weeks-long holdups while exposing the designs to intellectual property breaches.
- Molded Interconnect Devices (MIDs)
In its typical form, a MID is a 3D dielectric exoskeleton with electrical and mechanical functions combined in one component. Such a design can translate to dramatic improvements in size, shape or miniaturization of parts, all key in a rapidly changing aviation sector.
Using the DragonFly Pro to print MIDs has several benefits over both traditional structures and subtractive MID manufacturing methods.
First, the duration of each prototype iteration can be reduced from several weeks to about a day.
Second, the DragonFly Pro solves the traditional constraint of only being able to place electrically conductive traces on external surfaces of MIDs. With concurrent, multi-ink printing, conductive traces can be printed into the dielectric exoskeleton to enable further miniaturization and design customization, especially if electrical components such as resistors and quad-flat no-leads (QFNs) are embedded within the MID.
These specific advantages, coupled with time, cost and security improvements, positions the DragonFly Pro 3D Printer well to be a centerpiece of any aerospace manufacturing and R&D team.
- Endless Design Possibilities
Apart from producing existing designs with greater efficiency and security, Nano Dimension’s DragonFly Pro 3D Printer is also an important catalyst for creativity and innovation.
With the level of flexibility the DragonFly Pro offers in printing non-planar electronics and multi-layer PCBs, designers can print almost any functional electronic structures they can invent. Novel electronic elements, such as coils, antennas, electromagnets and flexible components, can also be included within the design and printed with minimal pauses for manual component placements.
This improves the likelihood of R&D teams realizing more breakthroughs and disruptive technologies, rather than making piecemeal improvements on existing products.
How would you fly higher with additive manufacturing?
For more information on how you can utilize the DragonFly Pro 3D Printer in your workflow, contact us via the link below.
Contact Us